The “butterfly effect” – the notion that a simple event in one area can have a dramatic effect elsewhere – can be seen every day in medical device development. A change that an engineer makes in a product design document reverberates throughout the organization, impacting Design Control, Risk Management, and Quality Assurance.
At least it should. But what if that design update isn’t picked up by others in the organization? What if, especially during the pandemic when people are working remotely, someone forgets to send an email or misses a voice mail message? What if someone refers to the wrong version of a requirement? The downstream impact will trigger the need for rework, with people scrambling to assemble documentation to submit to regulators or to provide to auditors – all of which wastes time and causes delays.
Disparate systems fall short
Regulations and quality standards imposed by the U.S. Food and Drug Administration (FDA), EU Medical Device Regulation (EU MDR), and the International Organization for Standardization (ISO) all specify that device manufacturers must establish and maintain procedures and records to control device design.
Too often, though, they rely on manual or disparate quality processes and systems that aren’t integrated. Disciplines work in siloes and critical information falls through the cracks. Different versions of documents drift around, and records are stored here, there, and everywhere, making it a monumental task to assemble them when needed. Despite everyone’s best intentions, the design process gets bogged down. And, since product design isn’t a one-and-done process, the issues are compounded over time.
Integrating key Quality processes
With an ecosystem of quality design processes supported by software modules that are fully integrated, information flows smoothly, work is synchronized, and everyone is referencing “one version of the truth.”
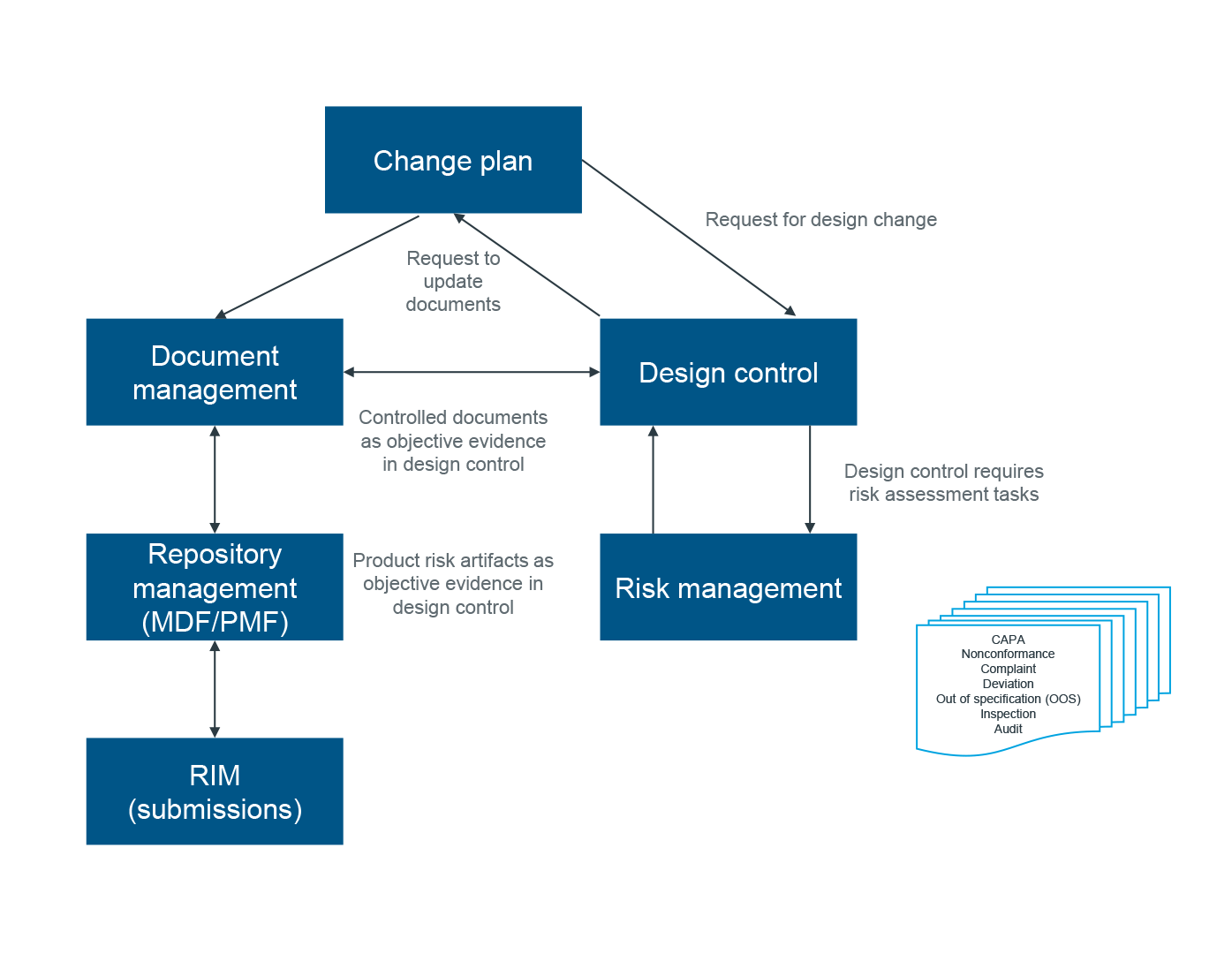
Here’s how it works. As the initial device design begins, all design documentation is maintained in one centralized repository, i.e., the Medical Device File. Policy-driven workflows ensure that appropriate information is recorded, reviewed, and approved according to regulatory requirements. This Design Control system is associated with a Risk Management module so that intended uses and any potential misuses are identified, and any harms, hazards, and hazardous situations are defined. The Product Risk File serves as the single source for all risk-related data for a given product.
The Medical Device File (MDF/PMF) repository includes all technical documentation for regulatory submission. All changes to design documentation and processes are recorded and managed via Change Management .
Changes to one part of the system are captured and cross-referenced throughout the ecosystem. Teams are notified of relevant changes. Reference documentation is retrievable. Reporting and analytics are automated. And, work is ushered along according to established workflows with any necessary “stage gates” in place.
A more efficient, consistent, and compliant process
When the design process for a device operates within such a framework where information is centralized and business rules guide the workflow, manufacturers and consumers benefit from
- Simplified collection, review, and approval of design evidence
- Fewer quality errors
- Reduced cycle times for registration and audits
- Demonstrated compliance with regulatory and legal requirements and industry best practices
- Consistent risk assessments that reveal a complete and accurate picture of risk for a given product
This integrated ecosystem ultimately ensures that quality management practices are employed to produce safe and effective medical devices in the most coordinated and efficient way possible.
Contact IQVIA to learn more about how SmartSolve® modules for Design Control, Risk Management, Document Management, and Change Management can speed your device development and improve your audit readiness.